German Digital Manufacturer Transforms Wheelchair Design with 3D Printing Innovation
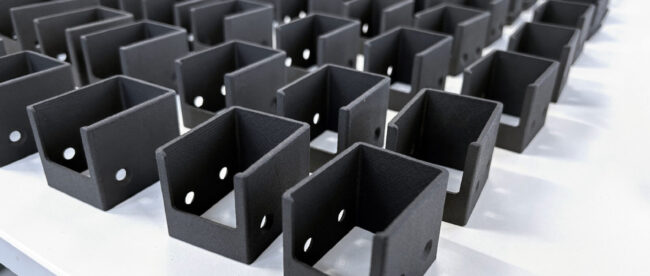
Replique, a German digital manufacturing company, partnered with RehaMedPower, a medical supplier specializing in wheelchairs, to revolutionize wheelchair design and production using HP’s Multi-Jet Fusion (MJF) technology. Traditional manufacturing methods for wheelchairs involved high costs and long lead times, but with 3D printing technology, Replique and RehaMedPower found a cost-effective and efficient solution. They discovered that they could manufacture many more wheelchair parts using 3D printing, reducing the need for expensive molds.
By utilizing MJF technology and digital design file storage through Replique’s platform, RehaMedPower achieved significant cost savings. They reduced development time by 30% and prototyping costs by 60% compared to injection molding. This not only benefits the company but also provides wheelchair users with more personalized care options. The RP1 wheelchair, designed with 3D printing, allows patients to customize various parts to their individual needs, offering flexibility in design and a wide range of colors.
The success of the RP1 wheelchair has led to its adoption across Europe and even in New Zealand. RehaMedPower plans to continue incorporating additive manufacturing (AM) designs into the RP1 wheelchair and develop new accessibility solutions. Additionally, they will soon offer on-demand production of spare parts through Replique’s global production network, ensuring patients have access to spare parts whenever and wherever they need them. This collaboration highlights the potential of 3D printing to provide customer-centric solutions in a cost-effective and flexible manner.
Image gallery (click to enlarge)
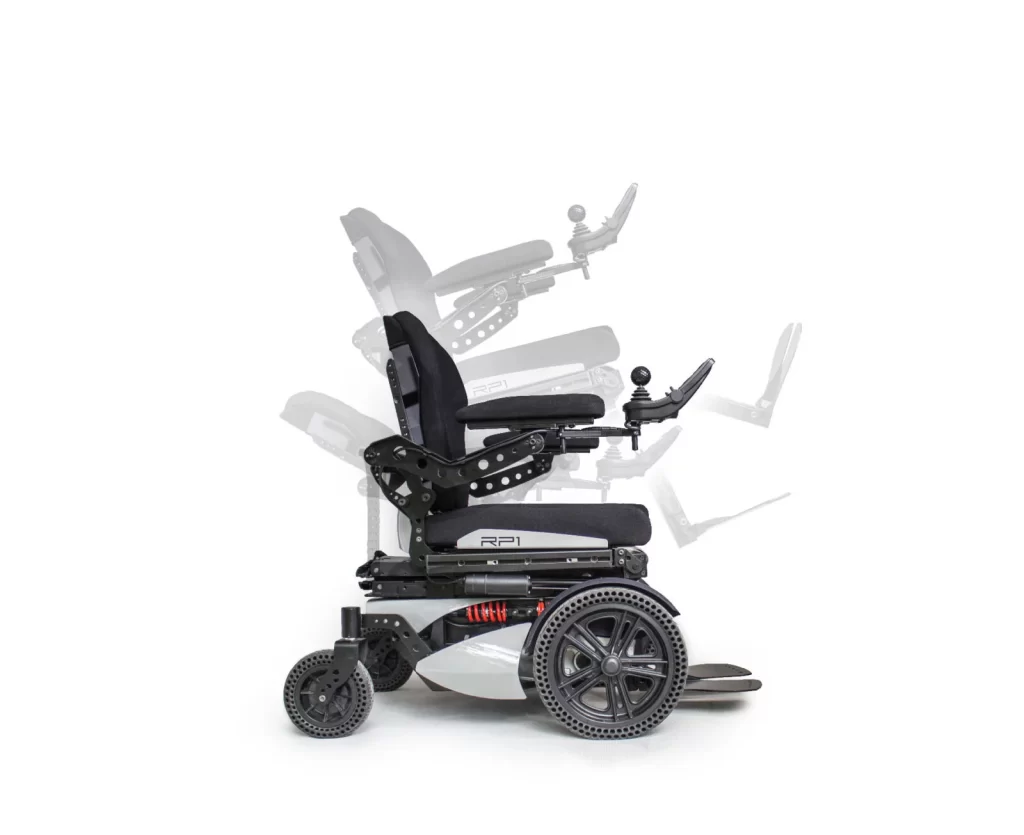

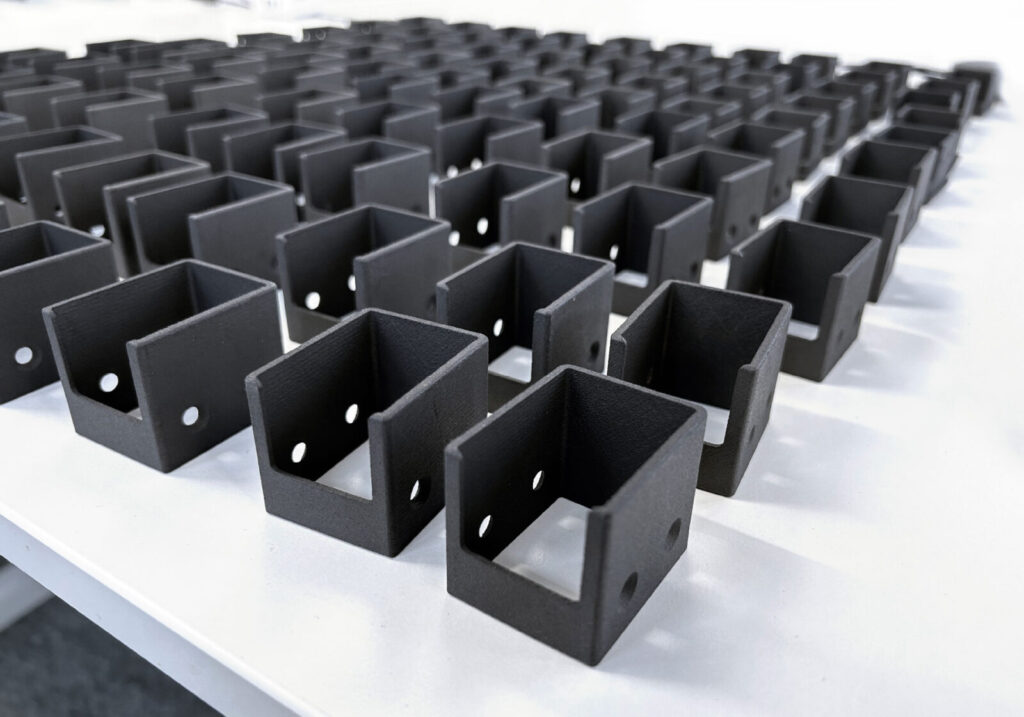
Source: Replique
What Is HP’s Multi-Jet Fusion Technology?
HP’s multi-jet fusion technology revolutionizes 3D printing by achieving exceptional part quality, speed, and cost-effectiveness. Through a proprietary process, it applies fusing and detailing agents to material layers, ensuring precise fusion and smooth edges. Temperature control is meticulously maintained across the material bed, granting control over mechanical properties and dimensional accuracy. This area-wide approach outperforms traditional point processing methods, offering predictable print times and the potential for multi-agent control of individual voxels, allowing for intricate, colorful, and functional 3D printed parts that push the boundaries of design and manufacturing.
Leave a comment